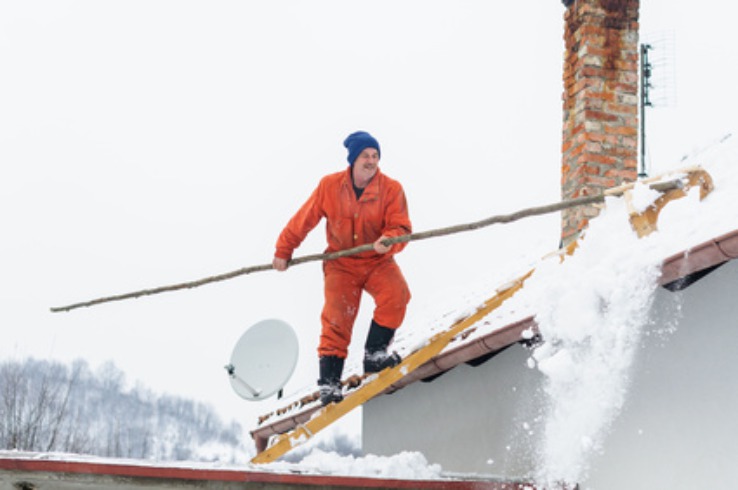
Workplace Safety - A Canadian Perspective
The Risk, The Response, The Reward
The Scope of the Problem
(SSN) - Canadians love their country. We pride ourselves on being peaceful, prosperous and progressive in many ways. We consistently rank at the top of many positive societal indices including “best country to live in”. However, unbeknownst to most of us, Canada is a dangerous place to work. We have one of the most hazardous countries to be employed in, according to a report by the International Labor Organization you can find here, When we compare ourselves to the other 29 countries in the Organization for Economic and Co-operative Development (OECD), Canada was ranked 25th with an unenviable fatality rate of 6.1 deaths per 100,000 workers. The only countries to score worse in this area were Korea (29.0), Turkey (20.6), Mexico (12.0), Portugal (8.7). In contrast, the American workers were almost twice as safe as Canadian ones with a 2012 rate of just 3.4 fatalities per 100K. Worse yet, most countries are experiencing a downward trend to their workplace death statistics while in Canada, they are actually rising.
How Safe Is My Province?
All of our provinces and territories are unique with their own focus on their regional industries, individual Workers Compensation Boards and challenges specific to each jurisdiction. As a result there is a huge difference in workplace fatality rates for each province and they are as follows:
- The Territories (NT, NU, YT) 27.4
- Newfoundland & Labrador 11.7
- British Columbia 8.9
- Alberta 8.0
- Ontario 6.5
- Nova Scotia 6.1
- Quebec 6.0
- Saskatchewan 5.6
- Manitoba 4.5
- New Brunswick 3.4 deaths
- Prince Edward Island 1.5
*Data as of 2005 courtesy of the Centre for the Study of Living Standards
Why Is There Such a Large Difference From Region To Region?
There are obviously a number of factors that influence these rates. Availability of medical care and distance to a hospital are enormous considerations which account for high fatality rates in non-urban occupations such as farming, mining, trapping and fishing.
As well, blue collar work is far more dangerous than occupations such as ‘finance’. This would at least partially account for the territories to be the ‘leader’ in this metric as there are far more blue collar, rural-based employment opportunities in territorial regions than office jobs.
The 10 Most Dangerous Jobs
As issued by Service Canada, the ten most dangerous jobs in the country were:
- Loggers: falling from trees, trees falling, cutting equipment.
- Fisheries workers: heavy equipment incidents, drowning.
- Pilots and flight engineers: air disturbances, high altitudes, takeoffs and landings.
- Roofers: falling, heat prostration from excessive temperatures.
- Structural iron and steel workers: falling, welding incidents, material handling.
- Waste management and sanitation workers: contact with dangerous material, heavy duty machinery, vehicular accidents.
- Electrical workers such as linesmen and wiring installers: electrocution, falling.
- Truck drivers and travelling sales staff: vehicular collisions, exhaustion.
- Farmers, ranchers, agrarian workers: heavy duty farm machinery, large animals.
- Construction workers: cutting and fastening equipment. falls
The Top Ten Ways We Get Hurt On The Job And Some Preventatives
Here are the ten most common causes of workplace injuries in descending order with the most prevalent method of injury being Number 1. As well are suggestions for reducing the rate of injury for each circumstance.
10. Assault from a co-worker
The HR management team has a role to play in preventing this sort of injury by knowing their employees and monitoring tension in the workplace. The use of peer boards to provide a body which employees can approach to settle interpersonal disputes have been shown to have a positive effect on the outcomes of negative workplace social dynamics.
9. Repetitive Motion Injuries
Whether twisting wrenches or typing reports, using the exact same muscles day in and day out is responsible for a number of negative health issues including back strain, vision problems and carpal tunnel syndrome. Having employees do a mix of actions during the day and insisting on appropriate breaks be taken can help.
8. Machinery Accidents
This sort of incident usually involves large, heavy machinery; forklifts and loaders, for example, which can easily crush a human. It can also include such equipment as paper shredders and other office machines. In all cases, however, the solution is for Human Resources to ensure all team leaders train every new hire in the operation of the equipment they will use in the course of their employment and the threats each machine may pose. Policy handbooks should be created and maintained that features best safety practices which must be required reading for all employees. Safety awards for accident-free operations are one option for keeping workplace safety in the forefront of the minds of staff members.
7. Vehicular Mishaps
Employees who drive on behalf of a company are at risk, like any other motorist, for getting into a crash causing injury. Managers must make it clear to employees that obeying traffic laws is imperative and not to give drivers unrealistic deadlines that cause them to speed or take other chances with their vehicles and their lives. A high tech solution could involve installing GPS monitors on all company vehicles that record the driving habits of those at the wheel.
6. Pedestrian collisions
A surprising number of on-the-job injuries are caused by employees walking into solid objects; walls, desk corners, doors, and glass partitions are just some examples. Some ways to reduce the hazard risk is to avoid office furniture with sharp corners, ensuring walkways are clearly marked and kept clear of large, stationary objects, as well as having proper lighting in your facility. Additionally, doors that push open should be well marked on the other side and have a small window to make sure there is no one walking into the door unexpectedly from the far side when opened suddenly.
5. Falling objects
A major cause of head, face and eye injuries result from objects falling from shelves or slipping from a hand or work surface from a great height, such as someone dropping a steel tool or similar item from a ladder. Strategies to prevent this type of incidence includes ensuring heavy items are stored lower than head height and those that cannot, be must be brought down with proper equipment such as a ladder cart. Those who work under a person on a ladder should always wear a hardhat.
4. Reaction injuries
This sort of damage, usually muscular in nature, results from a near fall or tripping on an obstacle with the harm arising from awkward twisting while trying to avoid hitting the floor. Sometimes the effort to stop from falling is actually more injurious than the fall might have been. This is a difficult cause to deal with other than employing the methods for reducing pedestrian collisions to prevent the near fall in the first place.
3. Falling from a height
This cause of workplace accidents is one of the most damaging, yet easiest to correct. Occupational Health and Safety rules are very clear as to the regulations surrounding employees working above ground height. Observing those rules through the proper use of fall-arrest equipment, handrails on elevated work stations, as well as constant monitoring to make certain guidelines are being followed, will play a big role in reducing this danger.
2. Falling on a same-level surface
This type of fall comes predominantly from slipping on wet or smooth surfaces and tripping over obstacles. Again, making sure walkways are free of hindrances is a huge step, as well as eliminating having any slick areas such as snowy walks or wet floors. Uneven walking surfaces are also a hazard for injuries of this nature. Another situation that leads to this sort of fall is when sitting on a wheeled chair that moves away as you sit. Making employees aware this is actually an extremely common cause of injury will alert them to the peril.
1. Overexertion
As much as employers want their staff to work hard and employees wish to complete tasks in a timely manner, overdoing a task is of no benefit to either party. The threat of overexertion is faced by office workers, plant workers and field staff alike. You can injure yourself just as easily trying to lift a box of steel as a case of bond paper. This is why lifting heavy items improperly, or trying to move weighty items without equipment is by far and away the leading cause of workplace injuries. Impressing on staff not to try and lift two-person loads with just one person or to use muscle power where machine power is required is one way to tackle this important problem. Human Resource associates have a large role to play in insisting employees work within their physical abilities with both initial training and ongoing monitoring.
The Bottom Line
Workplace safety is a shared responsibility of management and staff. The single-most important element a company can adopt to avoid injuries that are costly to both the business and the employees is to develop a culture of safety throughout the company. Corner cutting, even if it speeds up production, must be discouraged. Not only will creating a culture of safety potentially save you from expensive compensation or disability costs, public relations disasters and even criminal prosecution, it also helps with employee morale. When workers see that you value their lives, they are more likely to feel better about their employers. In all ways, diligent workplace safety is simply the right thing to do.
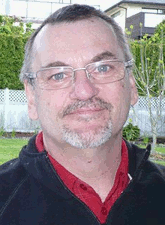